VA提案事例
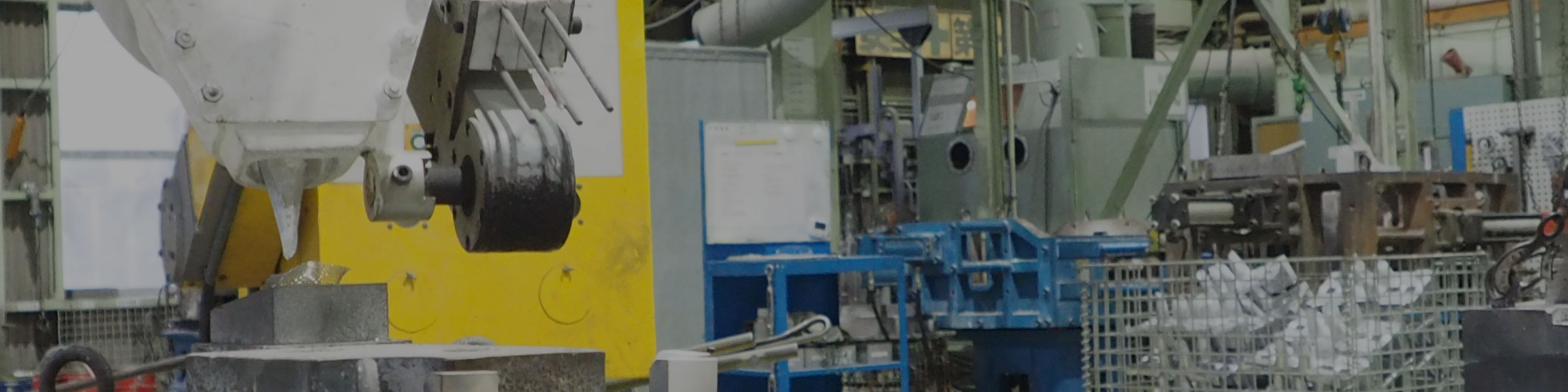
コストダウンにつながる事例
品質改善(鋳肌・強度・軽量化等)につながる事例
工具の摩耗を大幅に削減し、お客様の工具代の負担も軽減!
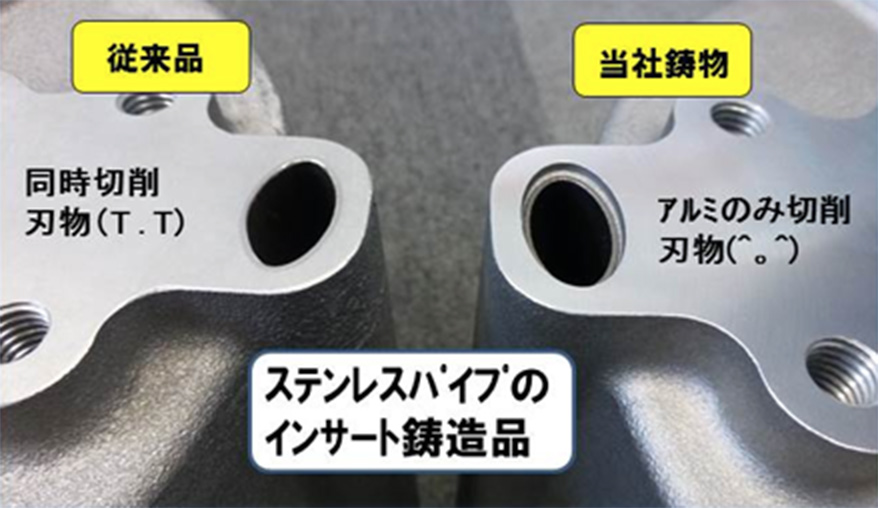
お困りごと
ステンレス製パイプを鋳ぐるみした製品です。従来品では面加工の際にアルミとステンレスを同時に切削加工していましたが、工具摩耗が激しく悩んでいます。
提案内容・結果
アルミ鋳物のみ削れるよう素材形状を改良し、工具の摩耗を大幅に削減。 お客様の工具代の負担も軽減できました。
バリ(カエリ)取り作業を無くし現場の作業負担を軽減!
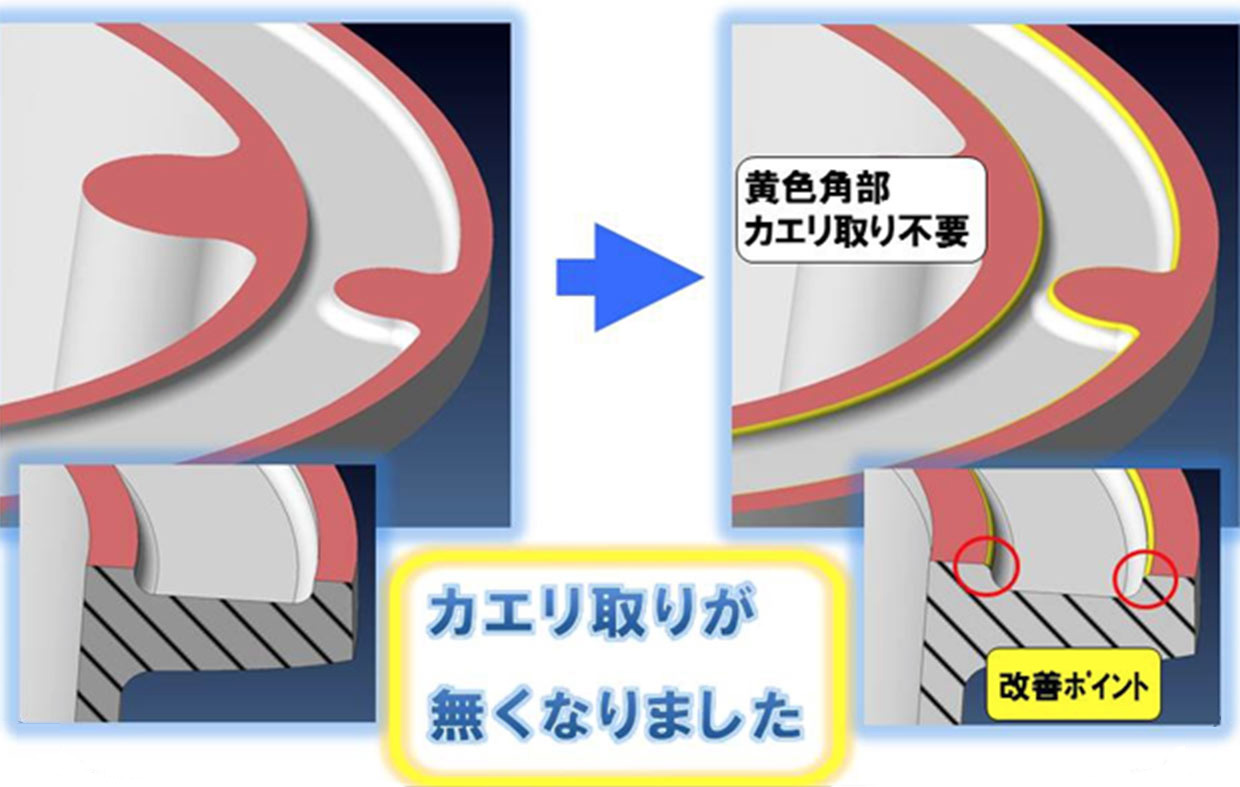
お困りごと
機械加工後、肉盗みの内側にバリ(カエリ)が生じてしまい、除去する手作業が増えてしまう。
提案内容・結果
バリ(カエリ)発生部にRを付け、段差形状に仕様変更。 加工面と鋳肌が上手く繋がり、バリ取り作業が不要になりました。お客様の作業負担軽減・製品の軽量化でコストダウンに成功しました。
ドリルでの穴あけ時に発生するバリ(カエリ)を無くし、面取り作業軽減!
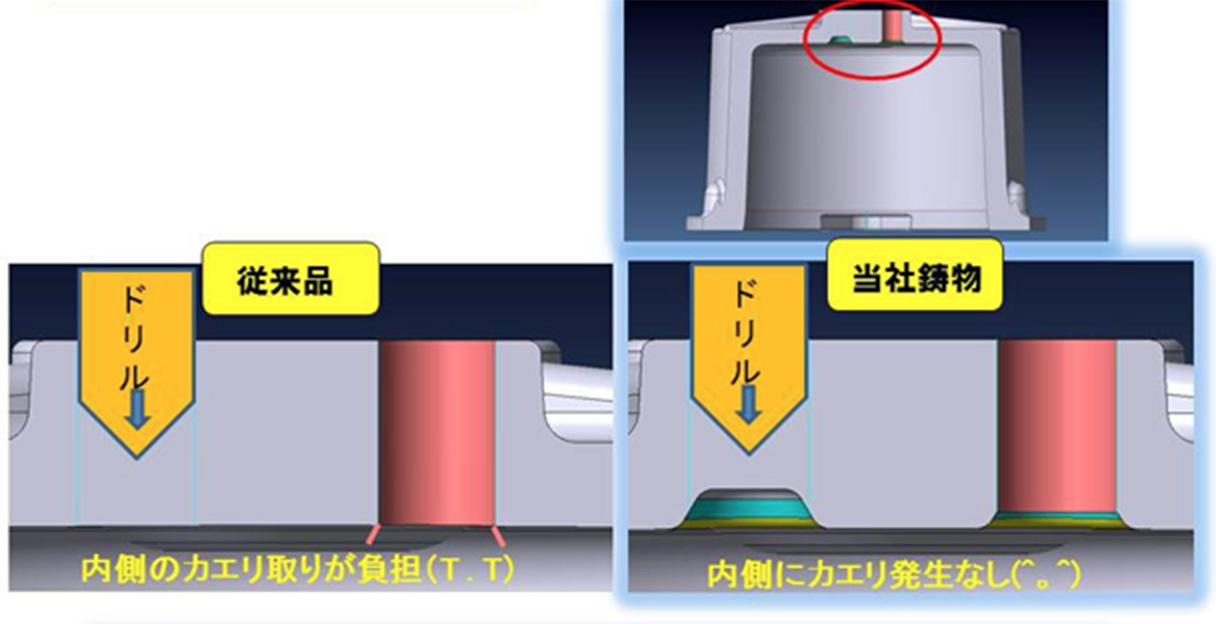
お困りごと
肉厚部へのドリルによる穴あけ加工後、バリ取りを行っています。バリ取り作業の負担を軽減したいのですが、良い方法はありませんか?
提案内容・結果
素材形状をキリ穴に繋がる接面形状にする事により面取り作業が軽減されました。
金型設計で加工レス化を図り、約28%のコスト低減!
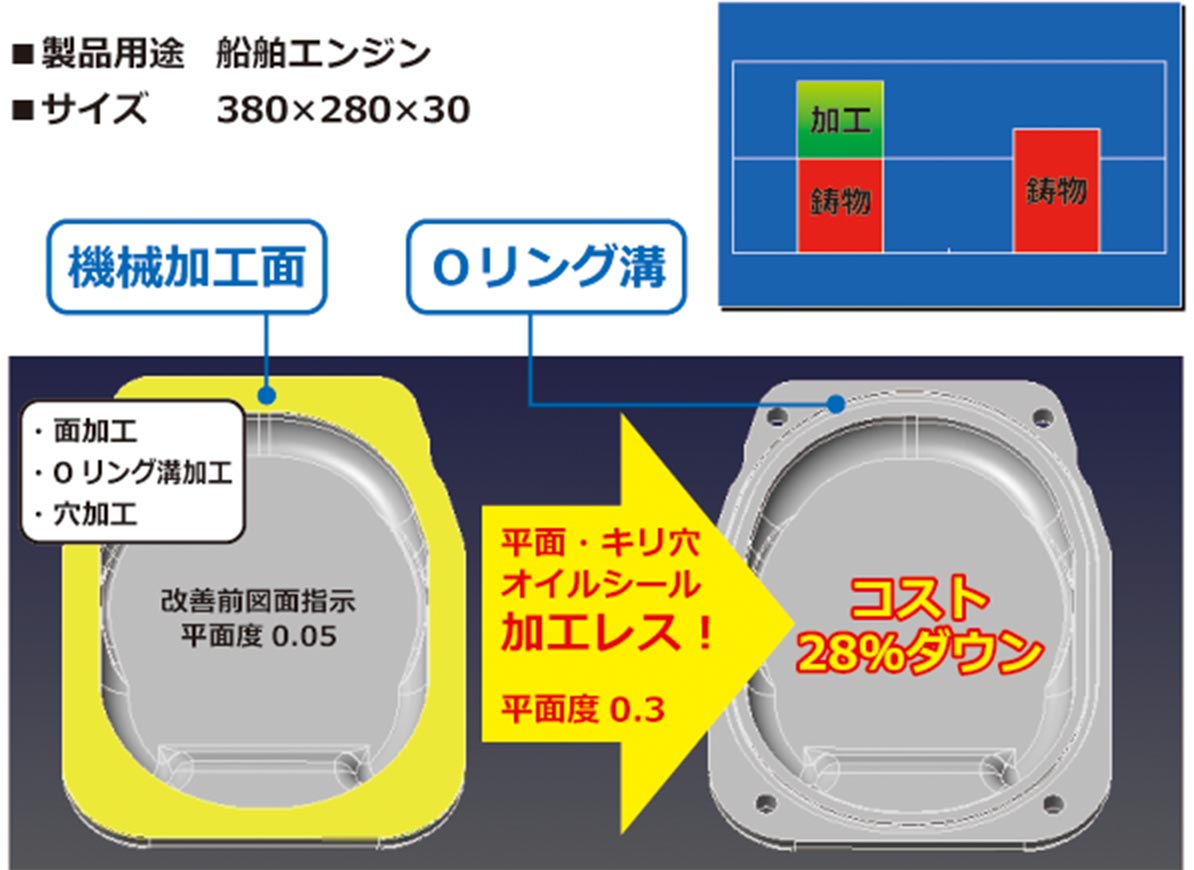
お困りごと
船舶エンジン部品のコスト削減を図っていますが、良いアイデアは無いでしょうか?
提案内容・結果
部品の要求制度によりますが、金型設計の際に加工レス化を図ることが可能です。今回は平面・キリ穴・オイルシールの加工レスにより約28%のコスト削減が可能でした。
自社独自の塗型メンテの工夫で鋳肌粗さが改善!
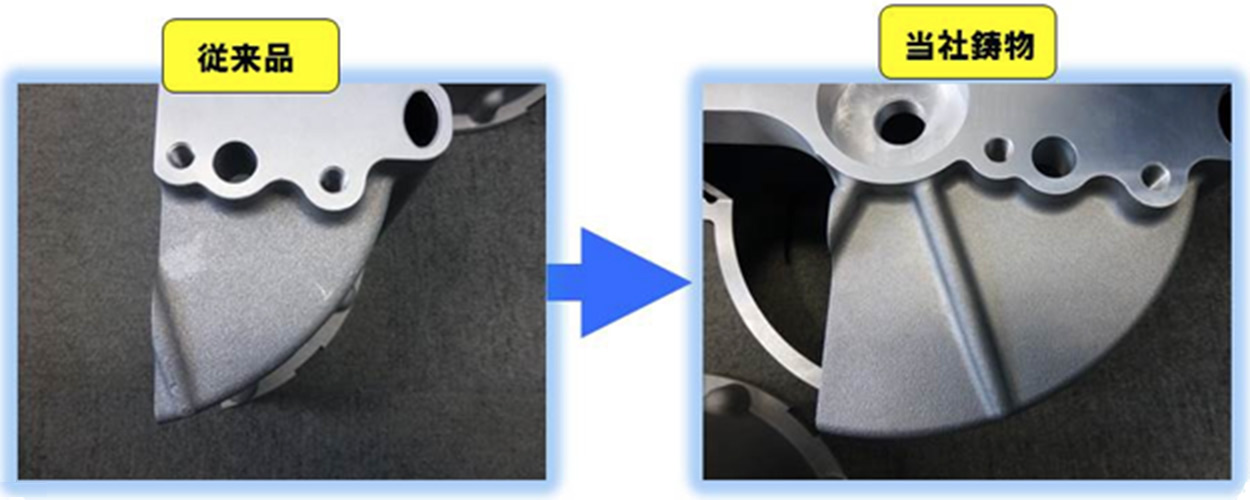
お困りごと
砂型・金型(グラビティ・低圧鋳造)鋳造で色々試したが鋳肌が粗く悩んでいます。
提案内容・結果
自社独自の塗型メンテ時に若干の工夫をした所、通常の手法より外観肌の見栄えも手触りも改善されました。
鋳肌改善により商品価値が向上!
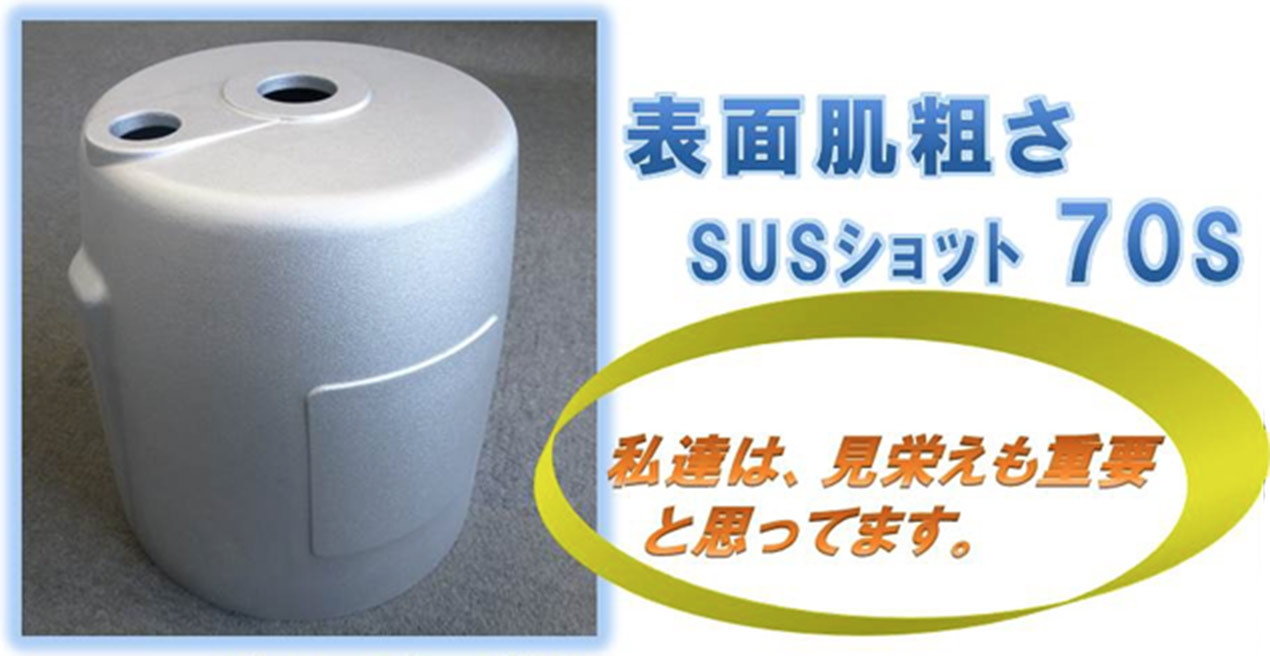
お困りごと
外寸:φ340mm、高さ307mm、肉厚:5mmの製品です。鋳造難易度が高い為、内面の欠陥と外観の鋳肌が粗い事に悩んでいます。
提案内容・結果
簡易金型鋳造と匠な職人技量・品質管理により安定した外観肌を実現。
微小巣を撲滅し内圧20Mpaの圧漏れゼロ!
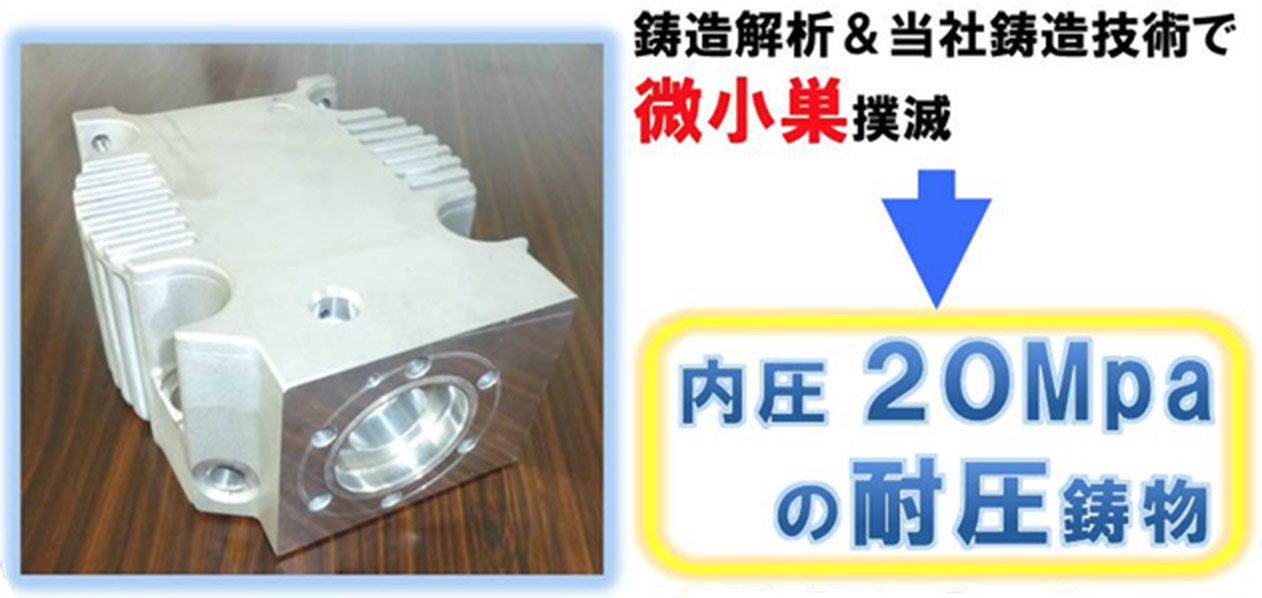
お困りごと
20メガパスカル(MPa)の内圧がかかる耐圧製品ですが、肉厚変動(凹凸)が大きく巣が生じやすく悩んでいます。
提案内容・結果
鋳造シミュレーションによる解析で原因を特定。無事、内圧20メガパスカル(Mpa)の圧漏れゼロを実現。
完全密着した異種金属のインサート(鋳ぐるみ)を実現!
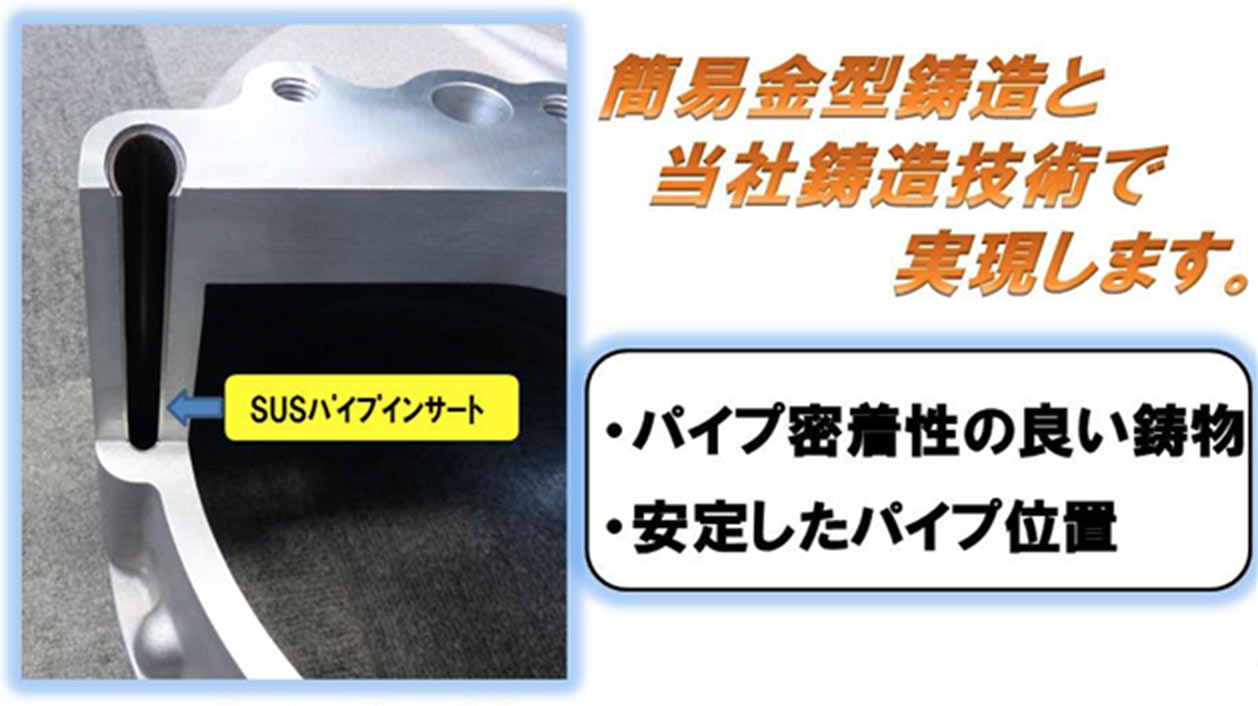
お困りごと
ステンレスパイプをインサート(鋳ぐるみ)した際、ガス溜まりによるブローホール(気泡)ができ易く悩んでいます。
提案内容・結果
安定したパイプ位置・密着性の良い鋳物製品を製造する事で、完全密着した異種金属のインサートを可能としました。
お問い合わせ・ご相談はこちら
〒929-1121 石川県かほく市宇気い6番地
TEL:076-283-4222
/FAX:076-283-2544
受付時間:平日8:00~17:00
お問い合わせフォーム